Nuts, seeds and dried fruit - we provide advice.
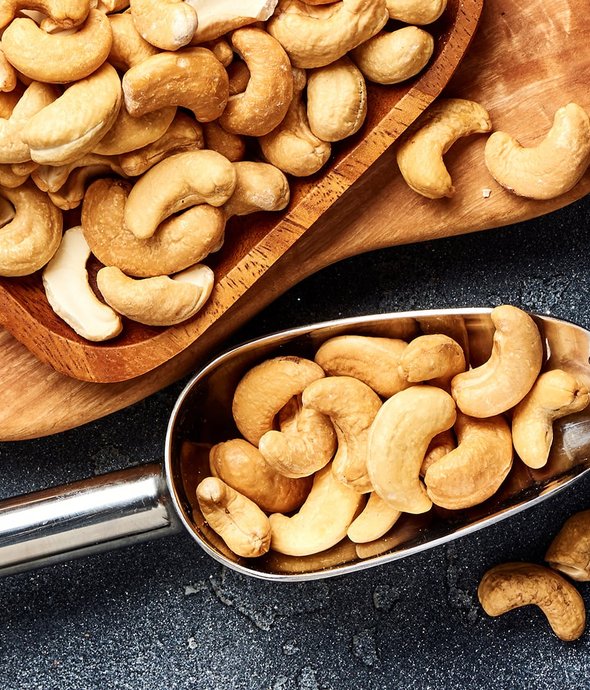
Services and advice
For decades, all our efforts have been focused on the cleaning, sorting and storage of seeds, nuts and dried fruits. In cooperation with our customers, suppliers and service providers, we have been able to optimize our processes and continuously improve the product quality. Experienced employees with long-term training provide these professional services on a storage and production area of 8000m².
We do not process peanuts, herbs and spices in our company.
Strengths and services
We will take care of your problems and find a solution.
At your request we will pick up your goods.
We examine your products, give an assessment and suggest solutions.
Our facilities are at the cutting edge of technology.
We place the quality standard very high and are still quick in the implementation.
We work in close cooperation with local authorities, such as customs, veterinary offices and laboratories.
We will arrange domestic and international transports for you quickly.
We process conventional and organic products.
2023
Back to old strength
The year 2023 is in full swing and so far we have achieved a lot:
- the large production halls were divided accordingly
- new machines and infrastructure were installed
- the workforce could be expanded
The company is very well positioned to meet future requirements.
2022
Restart
After the devastating major fire, a new production facility was found in 2022 and a modern machine park was set up. This puts us in a position to better implement the services we have offered so far.
2021
At the start of the year, the majority of the production site was destroyed in a large fire.
Management is making efforts to find a new production site to continue operation of the service company. The complex cleaning and treatment procedures were the products of decades of experience. These procedures were used to treat damaged products and make them ready for market again. As valuable food should not be wasted, management feels it has an obligation to avoid disposing of food prematurely. Our company has a second production facility, which has remained intact. This area is where our heat treatment procedure is performed.
With this low-temperature procedure, we can reduce germs, dry, mix, screen and roast products. A small scrubbing system and a chopping machine have already been purchased. Additional processes are currently being set up. The certification for IFS GMF will also have been completed by 2022.
2020
Number of employees
The company decided to train a fixed workforce. External staff have repeatedly caused damage in the past.
2019
On 1 January 2019, the company was renamed
changing its legal form from M. Visser eK to Visser Nutprocessing GmbH. All processes were carried over without any changes. All documents, forms and letterheads were changed.
All customers, suppliers, public authorities and agencies were notified in writing.
2018
Customer requirements are increasing
the aim is to maximise product safety while keeping costs low. In response, a tunnel metal detector was integrated into the process in 2018. This makes it possible to detect metal in goods weighing up to 25 kg even if they are packaged (in cardboard boxes, sacks, etc).
2016/17
Allergen policy & Chopping machine
To continue to meet our customers’ requirements, we put together an allergen policy.
As of 2016, the company M. Visser eK is officially authorised to treat products to kill any salmonella contamination. The authorisation process took over three quarters of a year, but the work paid off.
In 2017, we further developed and improved how we clean dried fruit. With a special chopping machine, we are able to chop dried fruit to the desired size.
2014/15
HACCP-Concept
To comply with customer requirements, we put together an HACCP plan. In preparation for certification of the company, M. Visser eK aimed to optimise, monitor and further improve its processes. Focus was given to product assurance and traceability as well as improving the product quality.
The disinfection procedure was further developed to optimise the cool-down phase.
2013
Rising quality requirements called for modernisation of the cleaning and processing systems
The entire production site was relocated to a modernised and larger building close by. Management invested in new technology – the cleaning systems that are still used today.
We are thus able to select impurities, for example plastic, stone, glass and metal. Even the separation of nutshells is no longer a problem, as the settings can be fine-tuned to allow even very small fragments to be removed.
The company brought in specialists to enable all employees to understand the new technical changes and make optimum use of them.
2008/10
Building for disinfection processes
Customer requests for disinfection processes were increasing, and management worked on this issue intensively. It quickly became clear that many disinfection methods were not suitable for fulfilling the product requirements. As the company specialises in nuts, dried fruit and seeds, extensive research into the wide range of possible disinfection methods was needed. A building was set up especially for the disinfection process, incorporating the latest technology.
2001
The company leased a new warehouse with 8,000 m² of usable floor space.
Entire containers were now delivered for cleaning. Storage business kept improving. In hindsight, it can be said that we were able to grow with our customers’ requirements.
As customer requirements increased, so did the administrative workload. With the knowledge he had garnered over the years, the business owner was constantly driven to test new processes that would help to meet the customers’ quality standards.
‘Stress batches’ (batches with freight or transport damage) were on the increase, so action needed to be taken urgently.
The office building had become too small to deal with the increasing administrative workload. Management invested in a new administration building.
The demand for processing of organically grown products was very high at this time. Management did everything it could to meet the requirements of the organic inspection body. From then on, the company also accepted commissions for treating and processing organic products. In this year, the demand for the treatment of stress batches increased. Quality management became increasingly important to ensure a high degree of product reliability.
1995
Company grew in size
In 1995, the company grew in size. Small quantities of seeds, nuts and dried fruit were cleaned, treated and processed.
To meet customer requirements, the company invested in machines and systems. These were turbulent times: the number of customers increased, goods volumes became bigger, and more and more orders were being placed.
Company management faced an important decision. It was going to be necessary to concentrate on one single line of business – all or nothing. The company would have to specialise either in storage and production work or in the import business. The business owner decided to discontinue the import business from the Far East and South America.
Attention was now entirely focused on cleaning and storing seeds, nuts and dried fruit.
1988
Increased storage capacity to 1,500 m²
In 1988, four years after the first warehouse was set up, storage capacity was increased to 1,500 m². The company now imported goods from the Far East and South America itself.
As demand was very high, attention was given to the cleaning of imported products. The source countries were visited to see how the product was grown and what kind of mechanical cleaning processes were used.
1984
Customer base increased
In 1984, the customer base increased and the office that had been set up on-site was converted into a small 300 m² warehouse with an adjacent office.
1983
Small office in Hamburg
In 1983, the owner independently opened a small office in Hamburg to better organise the transport between East and West Europe. The customer base at that time was mainly from the Netherlands.
The core business involved importing conserves, nuts and dried fruit for customers and shipping them to the Netherlands from Hamburg.
1966
Owner Marten Visser
In 1966, the current owner, Marten Visser, began working at his father’s company. He also learned his craft from the ground up, starting as a humble employee with dustpan and brush and working his way up to being a trade merchant.
1949
Customer orders with 36 lorries
In 1949, the business had expanded so much that customer orders with 36 lorries could be fulfilled. The core business involved the transport of conserves, coffee, cocoa and dried fruit.
1930
First lorry.
In 1930, the grandfather obtained his first lorry. The father of the current owner and his brother gradually joined the grandfather’s business and expanded the company into the transport sector, mainly transport by road.